Key Takeaways
1. Kaizen: The Foundation of Continuous Improvement
"Kaizen means 'continuous improvement.' The word implies improvement that involves everyone—both managers and workers—and entails relatively little expense."
Kaizen philosophy. Kaizen is a Japanese concept that emphasizes continuous, incremental improvements in all aspects of an organization. It involves:
- Small, ongoing changes rather than major overhauls
- Participation from all levels of employees
- Focus on process improvement rather than solely on results
- Low-cost, common-sense approaches
Benefits of kaizen:
- Increased productivity and efficiency
- Enhanced quality
- Reduced costs
- Improved employee morale and engagement
- Greater customer satisfaction
Kaizen is not a one-time event but a mindset and way of life that permeates the entire organization, fostering a culture of constant growth and adaptation.
2. Gemba: The Real Place Where Value is Created
"Gemba means 'real place'—the place where real action occurs."
Understanding gemba. In business, gemba refers to the actual workplace where value is created, such as:
- Factory floor
- Customer service center
- Sales floor
Importance of gemba:
- Direct observation of processes
- Immediate problem-solving
- Better understanding of customer needs
- Improved communication between management and frontline workers
Managers are encouraged to regularly visit the gemba to gain firsthand knowledge of operations, identify issues, and work collaboratively with employees to implement improvements. This hands-on approach, known as "gemba walks," ensures that decision-makers stay connected to the realities of their business and can make informed choices based on direct observation rather than relying solely on reports or secondhand information.
3. Quality, Cost, and Delivery (QCD): The Pillars of Business Excellence
"Quality, cost, and delivery (QCD) are not distinctly separate subjects but rather are closely interrelated."
QCD framework. This approach emphasizes the interconnectedness of these three critical aspects of business performance:
- Quality: Meeting or exceeding customer expectations
- Cost: Optimizing resources and reducing waste
- Delivery: Providing products or services on time and in the right quantity
Balancing QCD:
- Improving quality often leads to reduced costs and better delivery
- Focusing solely on cost-cutting can negatively impact quality and delivery
- Efficient delivery systems can improve both quality and cost performance
Organizations should strive for a balanced approach to QCD, recognizing that improvements in one area often positively impact the others. This holistic view helps companies achieve overall excellence and maintain a competitive edge in the market.
4. Standardization: The Key to Sustainable Improvement
"Standards become an integral part of gemba kaizen and provide the basis for daily improvement."
Role of standardization. Standardization involves establishing, communicating, and maintaining best practices across an organization. It is crucial for:
- Consistency in processes and outputs
- Easier identification of deviations and problems
- Facilitation of training and knowledge transfer
- Creating a baseline for further improvements
Implementing standards:
- Document current best practices
- Involve employees in creating and updating standards
- Make standards visual and easily accessible
- Regularly review and improve standards
Standardization is not about rigidity but about creating a stable foundation from which further improvements can be made. It allows organizations to capture and share knowledge, reduce variability, and continuously refine their processes.
5. 5S: Organizing the Workplace for Efficiency
"The five S (5S) are the five steps of workplace organization."
5S framework. This system for organizing and maintaining an efficient workplace consists of five Japanese words, each starting with 'S':
- Seiri (Sort): Remove unnecessary items
- Seiton (Set in order): Arrange necessary items for easy access
- Seiso (Shine): Clean and inspect the work area
- Seiketsu (Standardize): Create standards for the first three S's
- Shitsuke (Sustain): Maintain and improve the standards
Benefits of 5S:
- Increased productivity
- Improved safety
- Better quality control
- Enhanced employee morale
- Easier identification of problems
Implementing 5S creates a clean, organized, and efficient workplace that serves as a foundation for other improvement initiatives. It promotes a culture of discipline and continuous improvement among employees at all levels.
6. Muda: Identifying and Eliminating Waste
"Muda means 'waste' in Japanese. Any activity that does not add value is muda."
Types of muda. Taiichi Ohno, father of the Toyota Production System, identified seven types of waste:
- Overproduction
- Inventory
- Defects
- Motion
- Processing
- Waiting
- Transport
Eliminating muda:
- Train employees to identify different types of waste
- Encourage problem-solving at all levels
- Implement visual management to make waste visible
- Use tools like value stream mapping to analyze processes
By systematically identifying and eliminating muda, organizations can significantly improve efficiency, reduce costs, and enhance overall performance. The focus on waste elimination encourages a mindset of continuous improvement and resourcefulness among employees.
7. Visual Management: Making Problems Visible
"Visual management is a practical method for determining when everything is under control and for sending a warning the moment an abnormality arises."
Implementing visual management. This approach involves using visual cues to communicate information quickly and effectively:
- Color-coded signals
- Charts and graphs
- Kanban boards
- Andon lights
Benefits of visual management:
- Faster problem identification and resolution
- Improved communication across all levels
- Enhanced accountability and transparency
- Easier monitoring of performance and progress
Visual management transforms the workplace into an information-rich environment where abnormalities are immediately apparent. This allows for quick responses to issues and facilitates continuous improvement by making the current state of operations clear to everyone.
8. Just-in-Time Production: Optimizing Flow and Reducing Inventory
"JIT production aims at eliminating non-value-adding activities of all kinds and achieving a lean production system that is flexible enough to accommodate fluctuations in customer orders."
Key principles of JIT:
- Produce only what is needed, when it's needed, in the amount needed
- Minimize inventory at all stages of production
- Reduce setup times to allow for smaller batch sizes
- Create a smooth, continuous flow of materials and information
Benefits of JIT:
- Reduced inventory costs
- Improved cash flow
- Faster response to customer demands
- Higher quality due to quicker detection of defects
JIT production requires a highly coordinated and disciplined approach to manufacturing. It often involves techniques such as kanban systems, cellular manufacturing, and pull production to achieve a smooth, efficient flow of materials and products throughout the production process.
9. The Role of Leadership in Kaizen Implementation
"The role of top management should be to challenge all managers to attain ever higher goals."
Leadership responsibilities. Effective kaizen implementation requires strong leadership commitment:
- Set clear goals and expectations
- Provide necessary resources and support
- Lead by example in practicing kaizen principles
- Encourage and recognize employee contributions
Leadership actions:
- Regular gemba walks to stay connected with frontline operations
- Participate in improvement activities alongside employees
- Foster a culture of open communication and continuous learning
- Align organizational systems and structures to support kaizen
Leaders play a crucial role in creating and maintaining a kaizen culture. Their visible commitment and active participation are essential for inspiring employees and driving sustainable improvement throughout the organization.
10. Employee Empowerment: The Heart of Kaizen Culture
"Kaizen fosters process-oriented thinking because processes must be improved for results to improve."
Empowering employees. Kaizen relies on harnessing the knowledge and creativity of all employees:
- Provide training in problem-solving techniques
- Encourage employees to identify and solve problems
- Give frontline workers authority to make improvements
- Create systems for sharing ideas and best practices
Benefits of empowerment:
- Increased employee engagement and job satisfaction
- More innovative solutions to problems
- Faster implementation of improvements
- Better utilization of employee knowledge and skills
Employee empowerment is fundamental to creating a sustainable kaizen culture. By involving all employees in the improvement process, organizations can tap into a wealth of knowledge and creativity, leading to more effective and long-lasting improvements.
Last updated:
FAQ
What's Gemba Kaizen about?
- Continuous Improvement Focus: Gemba Kaizen by Masaaki Imai emphasizes the philosophy of continuous improvement, known as kaizen, particularly at the "gemba," the actual place where work is done.
- Practical Tools and Methodologies: The book provides practical tools and methodologies for implementing kaizen across various sectors, including manufacturing, healthcare, and service industries.
- Commonsense, Low-Cost Approach: Imai presents kaizen as a commonsense, low-cost management approach that can lead to significant improvements in quality, cost, and delivery.
Why should I read Gemba Kaizen?
- Proven Strategies: The book offers proven strategies for improving operational efficiency and effectiveness, making it a valuable resource for managers and leaders.
- Real-World Examples: Numerous case studies illustrate successful kaizen applications, helping readers understand the practical applicability of the concepts.
- Employee Empowerment: It emphasizes the importance of involving all employees in the improvement process, leading to higher morale and job satisfaction.
What are the key takeaways of Gemba Kaizen?
- Employee Engagement: Kaizen requires the involvement of everyone in the organization, from top management to frontline workers, for effective problem-solving.
- Gemba Focus: The book stresses the importance of going to the gemba to observe processes firsthand, helping managers understand workplace realities.
- Waste Elimination: A core principle is the elimination of waste (muda) in all forms, improving efficiency, reducing costs, and enhancing quality.
What is the definition of gemba in Gemba Kaizen?
- Actual Place: In Japanese, gemba means "the actual place" or "workplace," where value-adding activities occur.
- Central to Kaizen: The concept emphasizes the need for managers to observe and understand work processes directly for better problem identification.
- Cultural Significance: Being present at the gemba is crucial for effective management, fostering a culture of continuous improvement.
How does Gemba Kaizen define waste (muda)?
- Non-Value-Adding Activities: Waste (muda) is defined as any activity that does not add value to the product or service, such as unnecessary steps or defects.
- Seven Types of Muda: The book categorizes waste into seven types: overproduction, inventory, defects, motion, processing, waiting, and transport.
- Elimination Focus: The goal is to identify and eliminate these forms of waste to enhance productivity and quality.
What are the five steps of 5S in Gemba Kaizen?
- Seiri (Sort): Distinguish between necessary and unnecessary items, discarding the latter to declutter the workspace.
- Seiton (Set in Order): Organize necessary items efficiently, ensuring each has a designated place for easy access.
- Seiso (Shine): Emphasize cleaning and maintaining cleanliness to identify abnormalities and ensure effective equipment operation.
- Seiketsu (Standardize): Establish standards for the first three steps to maintain organization and cleanliness over time.
- Shitsuke (Sustain): Foster self-discipline to maintain established standards, encouraging a culture of continuous improvement.
What are the golden rules of gemba management in Gemba Kaizen?
- Go to the Gemba First: Managers should start by going to the gemba when a problem arises for better understanding and decision-making.
- Check the Gembutsu: Examine relevant objects related to the problem to identify root causes.
- Take Temporary Countermeasures: Implement immediate solutions on the spot while developing permanent ones.
- Find the Root Cause: Investigate and identify the root cause of problems to prevent recurrence.
- Standardize to Prevent Recurrence: Standardize new procedures to ensure the same issue does not happen again, creating a continuous improvement cycle.
What role does management play in Gemba Kaizen?
- Leadership in Kaizen: Management must demonstrate commitment and involvement in kaizen initiatives, actively participating in improvement activities.
- Setting Clear Targets: Managers are responsible for establishing clear quality, cost, and delivery targets to guide kaizen efforts.
- Empowering Employees: Management should empower employees to take ownership of their work processes and encourage participation in kaizen activities.
- Providing Resources: Ensure teams have the necessary resources, training, and support to implement kaizen effectively.
- Monitoring and Evaluating: Monitor progress and evaluate the effectiveness of kaizen initiatives to identify areas for further improvement.
How does Gemba Kaizen suggest implementing continuous improvement?
- Start with Training: Train employees in kaizen principles and tools to empower them to identify and solve problems.
- Use of Kaizen Events: Organize kaizen events where cross-functional teams focus on specific improvement projects.
- Measure and Standardize: Support continuous improvement with objective measurements and standardized processes to sustain and build upon improvements.
What are some best practices for implementing kaizen from Gemba Kaizen?
- Start Small: Begin with small, manageable kaizen projects to demonstrate quick wins and build momentum.
- Involve Everyone: Engage all employees in the kaizen process, fostering a sense of ownership and commitment to improvement.
- Use Visual Management: Implement visual management techniques to make problems and progress visible, keeping everyone informed.
- Encourage Suggestions: Create a suggestion system for employees to share improvement ideas, recognizing and rewarding contributions.
- Continuous Training: Provide ongoing training to develop skills and understanding of kaizen principles, sustaining a culture of continuous improvement.
How can Gemba Kaizen be applied in non-manufacturing sectors?
- Adaptation of Principles: Kaizen principles can be adapted to any industry, including healthcare, education, and service sectors.
- Gemba Walks: Conduct gemba walks in non-manufacturing settings to observe workflows and identify inefficiencies.
- Cross-Functional Teams: Form cross-functional teams to address specific challenges, leveraging diverse perspectives for innovative solutions.
What challenges might organizations face when implementing Gemba Kaizen?
- Resistance to Change: Employees may resist adopting new practices, requiring effective communication and leadership support to overcome.
- Lack of Training: Insufficient training in kaizen principles can hinder improvement initiatives, necessitating comprehensive training programs.
- Sustaining Improvements: Maintaining momentum and ensuring sustained improvements can be challenging, requiring clear metrics and regular reviews.
Review Summary
Gemba Kaizen receives mostly positive reviews for its practical approach to continuous improvement. Readers appreciate the real-world examples and case studies, though some find them repetitive. The book is praised for its accessibility and focus on low-cost, common-sense strategies. Critics note that while it's an excellent introduction to Kaizen principles, it may lack depth for experienced practitioners. The emphasis on employee involvement and the importance of making improvements at the source (gemba) are highlighted as key strengths.
Similar Books
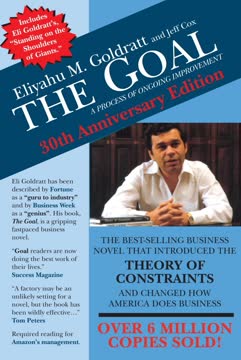
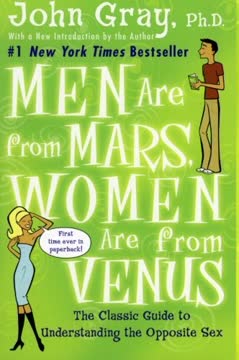
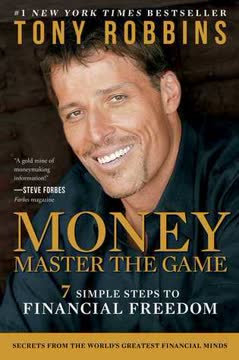
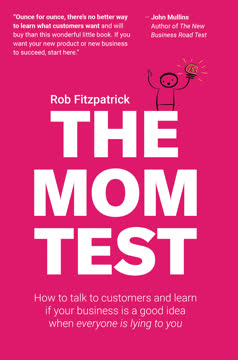
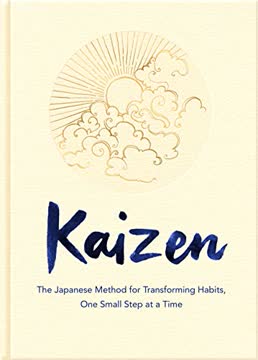
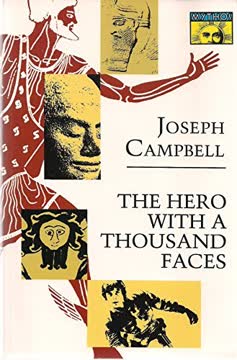
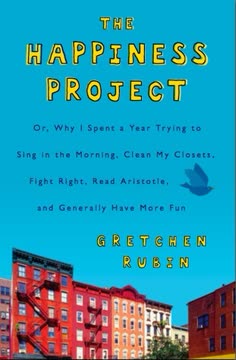
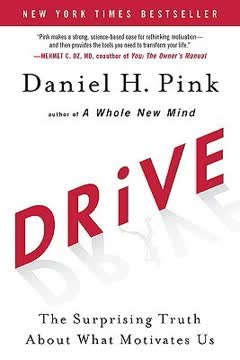
Download PDF
Download EPUB
.epub
digital book format is ideal for reading ebooks on phones, tablets, and e-readers.