Key Takeaways
1. Value Stream Mapping: A Strategic Tool for Organizational Transformation
Value stream mapping becomes an important step in using the Plan-Do-Study-Adjust (PDSA) cycle to solve performance issues, capitalize on market opportunities, plan new product lines, and improve existing ones.
Holistic view of processes. Value stream mapping is a powerful methodology for visualizing and improving how work flows through an organization. It provides a macro-level view of the entire process from customer request to delivery, revealing inefficiencies, bottlenecks, and opportunities for improvement.
Strategic alignment and cultural shift. Beyond just a tool, value stream mapping serves as a foundation for Lean business management. It aligns leadership, builds consensus, and drives organizational transformation by instilling a customer-centric, holistic thinking mindset. The process of mapping itself often leads to significant cultural shifts, changing how people think about and approach their work.
Key benefits:
- Visualizes complex work systems
- Identifies disconnects, redundancies, and gaps
- Drives data-driven decision making
- Connects disparate parts of the organization
- Provides a blueprint for improvement
- Orients new hires to organizational processes
2. Preparing for Value Stream Mapping: Setting the Stage for Success
To fully leverage the power of value stream mapping, we recommend you avoid these common failings.
Thorough planning is crucial. Successful value stream mapping begins with careful preparation. This includes developing a clear charter, building leadership support, forming the right team, collecting relevant data, and preparing the organization for transformation.
Key elements of preparation:
- Develop a detailed charter outlining scope, objectives, and timelines
- Select a cross-functional team with authority to make changes
- Educate participants on value stream mapping principles
- Collect baseline data on current performance
- Prepare the workforce for the mapping process and potential changes
Avoiding common pitfalls. Many organizations fail to reap the full benefits of value stream mapping due to inadequate preparation or misuse of the methodology. Common mistakes include using mapping solely as a work design exercise, focusing on tactical rather than strategic improvements, and failing to take action on the insights gained.
3. Understanding the Current State: Discovering How Work Really Flows
Gaining a deep understanding of current state value stream performance is a vital step in designing and making improvement.
Go to the gemba. A critical step in creating the current state map is physically walking the value stream, known as "going to the gemba." This allows the team to observe work directly, talk to workers, and gain firsthand insights into obstacles and inefficiencies.
Documenting the current state involves:
- Walking the value stream (twice if possible)
- Laying out the basic process flow
- Collecting key metrics for each process:
- Process Time (PT)
- Lead Time (LT)
- Percent Complete and Accurate (%C&A)
- Identifying barriers to flow
- Mapping information flow
- Calculating summary metrics
Unveiling the truth. The current state map serves as a visual storyboard that reveals how work actually gets done, often for the first time. This shared understanding of reality is crucial for building consensus around the need for change and identifying opportunities for improvement.
4. Designing the Future State: Creating a Blueprint for Improvement
Remember that value stream maps serve as visual storyboards that not only clarify how work gets done, but also reveal problems.
Envisioning improvement. The future state design phase is where the team innovates and creates a vision for how the value stream should operate. This involves challenging existing paradigms and thinking creatively about how to deliver greater value to customers more efficiently.
Key considerations for future state design:
- Determining the "right work" to be done
- Making work flow without delays
- Managing the work to achieve continuous improvement
- Applying Lean principles and countermeasures
- Balancing aggressiveness with achievability
Measurable targets. The future state map should include specific, measurable targets for improvement in key metrics such as lead time, process time, and quality. These targets drive the transformation plan and provide a way to measure success.
5. Developing the Transformation Plan: Turning Vision into Action
The purpose of value stream mapping is to improve the value stream.
Action-oriented planning. The transformation plan bridges the gap between the future state vision and reality. It outlines specific actions, responsibilities, and timelines for implementing improvements.
Key elements of the transformation plan:
- Measurable targets for each improvement
- Proposed countermeasures (improvements)
- Execution method (Just-Do-It, Kaizen Event, Project)
- Owner for each improvement
- Timeline for execution
- Status tracking mechanism
Gaining buy-in. Socializing the transformation plan with leadership and affected stakeholders is crucial for success. This builds understanding, reduces resistance to change, and ensures necessary resources are allocated.
6. Executing Improvements: Making Change Happen
Outstanding organizations possess the discipline to execute the plan as designed unless—borrowing from law—the "preponderance of the evidence" indicates that modification is needed.
Disciplined execution. Implementing the transformation plan requires focus, discipline, and the ability to adapt as new information emerges. Regular progress reviews help keep the transformation on track and allow for course corrections when needed.
Key aspects of execution:
- Following the scientific method (PDSA) for each improvement
- Conducting regular transformation plan reviews
- Addressing obstacles and resistance as they arise
- Adjusting the plan when necessary based on new information
- Celebrating successes and learning from setbacks
Balancing flexibility and focus. While it's important to stick to the plan, teams must also be prepared to adjust based on real-world results and changing conditions. The key is finding the right balance between discipline and adaptability.
7. Sustaining and Continuously Improving: Embedding Value Stream Thinking
We're often asked how frequently a value stream should be improved. The answer is continuously.
Sustaining gains. Maintaining improvements requires robust management systems, clear accountability, and ongoing measurement. Designating a value stream manager to oversee performance and drive ongoing improvement is crucial.
Elements of sustainable improvement:
- Clearly defined key performance indicators (KPIs)
- Regular monitoring and reporting of value stream performance
- Designated value stream manager or champion
- Empowered workforce trained in problem-solving
- Culture of continuous improvement
Continuous improvement cycle. Value stream mapping should be an ongoing process, not a one-time event. Regular reviews and remapping (at least annually) help organizations continue to raise the performance bar and adapt to changing conditions.
Cultural transformation. Ultimately, value stream mapping and management should become embedded in the organization's DNA, shifting mindsets from siloed thinking to holistic, customer-focused improvement. This cultural change is the key to sustained excellence and competitiveness.
Last updated:
FAQ
What's "Value Stream Mapping: Using Lean Business Practices to Transform Office and Service Environments" about?
- Purpose of the book: The book by Karen Martin and Mike Osterling is a comprehensive guide on using value stream mapping to improve business processes in office and service environments.
- Focus on Lean principles: It emphasizes Lean business practices to streamline operations, reduce waste, and enhance customer value.
- Application beyond manufacturing: While value stream mapping is traditionally used in manufacturing, this book adapts the methodology for non-manufacturing settings.
- Strategic transformation tool: The authors present value stream mapping as a strategic tool for enterprise-wide transformation and organizational alignment.
Why should I read "Value Stream Mapping" by Karen Martin?
- Holistic approach: The book offers a holistic approach to understanding and improving business processes, which can lead to significant performance improvements.
- Practical guidance: It provides step-by-step instructions and real-world examples, making it accessible for both beginners and experienced practitioners.
- Cross-industry relevance: The principles and techniques discussed are applicable across various industries, including healthcare, finance, and government.
- Organizational benefits: Implementing the strategies can lead to improved efficiency, reduced costs, and enhanced customer satisfaction.
What are the key takeaways of "Value Stream Mapping"?
- Value stream mapping as a tool: It is a powerful methodology for visualizing and improving the flow of work across an organization.
- Importance of current state analysis: Understanding the current state of processes is crucial for identifying areas of improvement.
- Future state design: The book emphasizes designing a future state that eliminates waste and enhances value delivery.
- Continuous improvement: It advocates for ongoing evaluation and refinement of processes to sustain improvements.
How does "Value Stream Mapping" define a value stream?
- Sequence of activities: A value stream is defined as the sequence of activities an organization undertakes to deliver on a customer request.
- Cross-functional nature: It typically involves multiple departments and functions working together to produce a good or service.
- Inclusion of information flow: The value stream includes both the flow of materials and information necessary to complete the process.
- Extended value stream: It may also encompass activities that occur before and after the main production or service delivery.
What is the role of a value stream map according to Karen Martin?
- Visual representation: A value stream map provides a visual representation of how work flows through an organization.
- Identification of waste: It helps identify areas of waste, inefficiencies, and bottlenecks in the process.
- Strategic planning tool: The map serves as a foundation for strategic planning and decision-making to improve processes.
- Alignment and communication: It facilitates alignment and communication across different functions and levels of the organization.
How does "Value Stream Mapping" suggest improving work flow?
- Eliminate waste: Focus on removing unnecessary steps and activities that do not add value to the customer.
- Standardize processes: Implement standard work practices to ensure consistency and reduce variability.
- Enhance quality: Build quality at the source to prevent defects and rework.
- Implement pull systems: Use pull systems to ensure work is only done when there is demand, reducing overproduction and inventory.
What are some common pitfalls in value stream mapping according to the book?
- Using it as a tool only: Treating value stream mapping solely as a tool rather than a strategic methodology can limit its effectiveness.
- Lack of leadership involvement: Failing to involve leaders who can authorize change can stall or derail improvement efforts.
- Inadequate data collection: Not collecting sufficient data can lead to incomplete or inaccurate maps.
- Ignoring cultural aspects: Overlooking the cultural and behavioral changes needed to sustain improvements can result in backsliding.
What are the best quotes from "Value Stream Mapping" and what do they mean?
- "Very few things are unmanageable once they are distilled to their basic components." This quote emphasizes the power of simplification in managing complex processes.
- "No complex journey should start without a map." It highlights the importance of having a clear plan and understanding of the current state before embarking on improvements.
- "The broader use of value stream mapping as a methodology to transform leadership thinking, define strategy and priorities, and assure that customers are receiving high levels of value." This underscores the strategic role of value stream mapping beyond just process improvement.
How does "Value Stream Mapping" address the role of leadership?
- Leadership engagement: Leaders must be actively involved in the mapping process to drive change and ensure alignment with strategic goals.
- Decision-making authority: Leaders on the mapping team should have the authority to make decisions and implement changes.
- Cultural transformation: Leadership plays a crucial role in fostering a culture of continuous improvement and Lean thinking.
- Ongoing support: Leaders need to provide ongoing support and resources to sustain improvements and address any obstacles.
What is the significance of the current state map in "Value Stream Mapping"?
- Baseline understanding: The current state map provides a baseline understanding of how processes currently operate.
- Identification of issues: It helps identify inefficiencies, bottlenecks, and areas of waste that need to be addressed.
- Foundation for improvement: The current state map serves as the foundation for designing the future state and planning improvements.
- Consensus building: It facilitates consensus among stakeholders on the need for change and the areas to focus on.
How does "Value Stream Mapping" suggest handling freed capacity?
- Absorb additional work: Use freed capacity to handle increased demand without adding more staff.
- Reduce overtime: Lower the need for overtime by optimizing existing resources.
- In-source work: Bring outsourced work back in-house to utilize available capacity.
- Focus on innovation: Allocate freed capacity to innovation and continuous improvement activities.
What are the recommended steps for developing a transformation plan in "Value Stream Mapping"?
- Define measurable targets: Clearly outline the objectives and expected outcomes of the transformation.
- Identify countermeasures: List the improvements needed to achieve the future state design.
- Assign ownership: Designate responsible individuals for each improvement action.
- Set timelines: Establish a timeline for executing improvements and regularly review progress.
Review Summary
Value Stream Mapping receives mostly positive reviews, with an average rating of 3.96/5. Readers appreciate its practical approach to strategic planning and change management. The book is praised for its detailed guidance on conducting value stream mapping workshops and its focus on high-level, strategic improvements. Some reviewers note that while the mapping process is well-explained, the implementation phase is less prescriptive. Critics mention that the book can be repetitive and may require additional research for effective implementation. Overall, it's considered a valuable resource for those interested in Lean principles and organizational improvement.
Similar Books
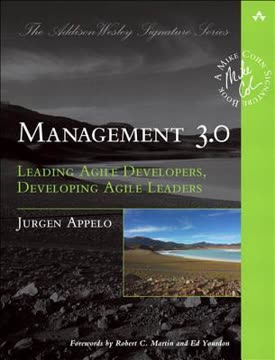
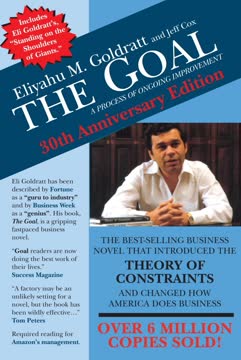
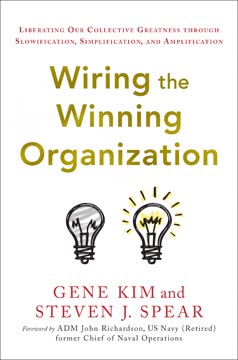
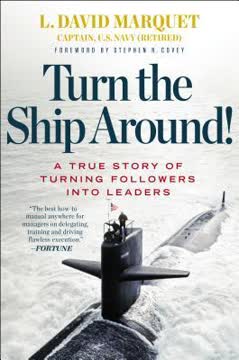
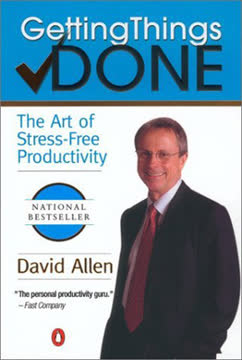
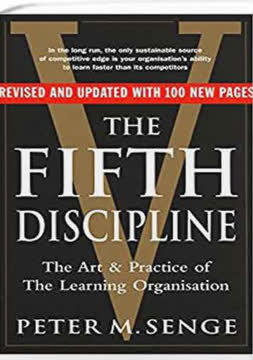
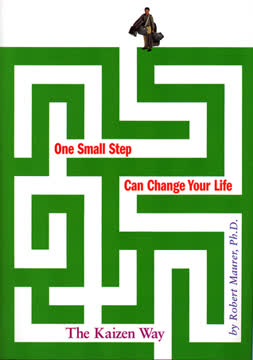
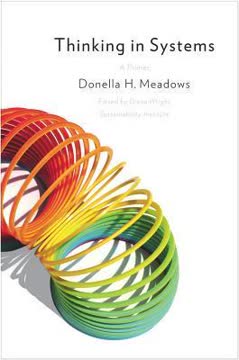
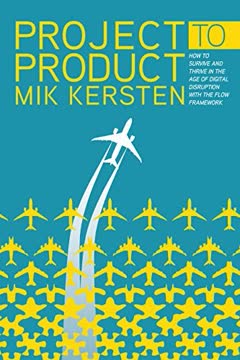
Download PDF
Download EPUB
.epub
digital book format is ideal for reading ebooks on phones, tablets, and e-readers.